Three-dimensional (3D) printing is the latest big innovation in textile design and manufacturing, with the world of high-end fashion showing significant interest in 3D printing directly onto base fabrics.
Flexible design
3D printing provides aesthetic freedom with microscopic accuracy.
Minimise waste
3D printing reduces waste as there is little to no off-cut waste in the garment construction processes.
Infinite potential
3D printing enables designers to achieve complex shapes and textures as well as intricate details and delicate decorative features.
The latest 3D printing technology is very suitable for use on fabrics made from the world’s most technical natural fibre, Merino wool.
Designers can combine the aesthetic freedom of 3D printing while maintaining the supreme comfort, beautiful drape, and natural performance of Merino wool and wool blend fabrics.
HOW IT WORKS
3D printing
Today’s 3D printing technology produces microscopic accuracy. Designers have complete freedom to create as complex shapes and textures as they desire. Intricate details and delicate decorative features are possible.
As well as using complex shapes, designers can incorporate the widest variety of colours, including multi-colours, unique gradient colours and transparency.
3D printing on the base fabric can create new visual appearances such as enigmatic shimmer effects when the garment moves on the body.
Production times and environmental costs (less waste) can be minimised thanks to the integration of technology into the design process.
There are also endless possibilities for customisation and personalised design.
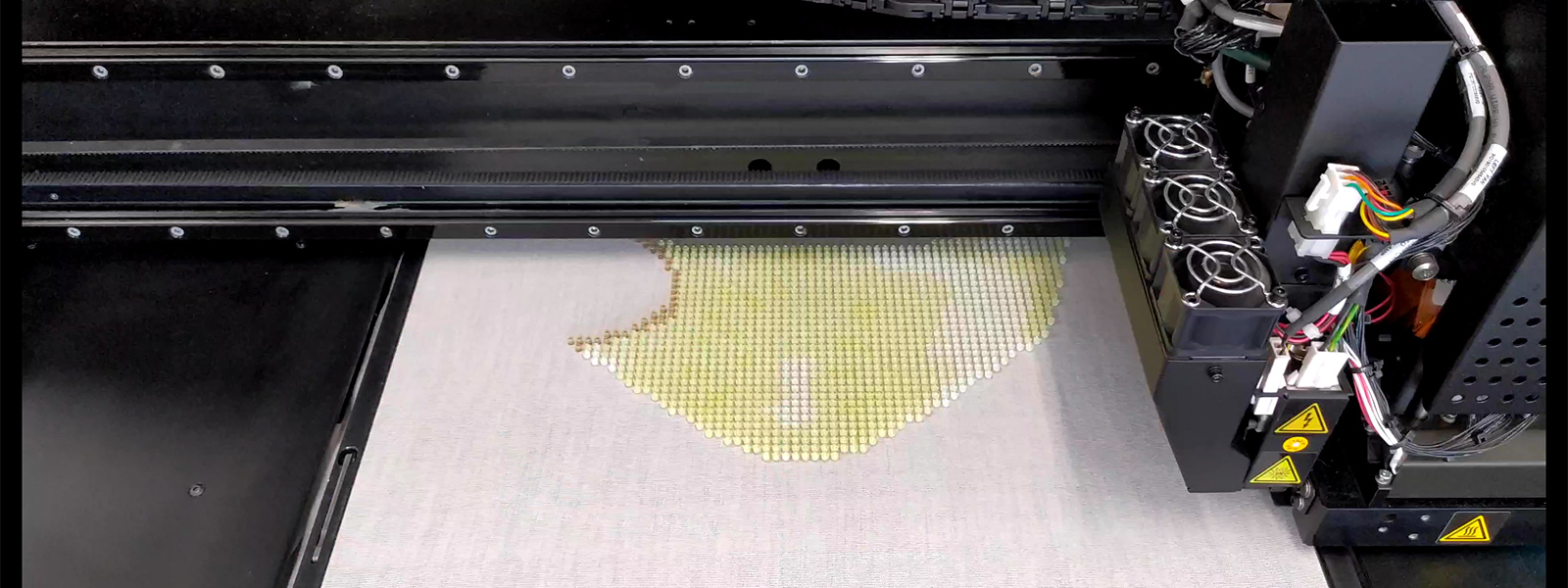
Partners using 3D printing
D-house, urban laboratory by Dyloan
D-house, urban laboratory by Dyloan, has been researching and applying 3D printing technology on Merino wool fabric. To show the versatility of the possible applications, the company undertook a ‘Knitting the future - 3D printing meets Merino wool’ project in collaboration with The Woolmark Company and manufacturer of 3D printers, Stratasys.
The project involved three international designers and four students from the Royal College of Art in London creating 3D printed designs on Merino wool knitwear that were produced at Dyloan’s production facility Bond Factory.
The three international designers were Italian creative and experimental knitwear designer Vittorio Branchizio, Italian trans-media artist and designer Matteo Cibic and London-based knitwear designer Laura Theiss. The four students from the Royal College of Art were Katharina Dubbick, Amaranthe Frost, Oliver Hurdman and María Fernanda Nava.
The project was supported by yarn suppliers; Manifattura Sesia, Tollegno 1900, Zegna Baruffa Lane Borgosesia, Südwolle Group, CoatYarn, Expotex and Fulgar and knitters; Alessandro Simoni, Artemaglia, Effebi, Mas, Miles and Ribknit.